Can alumina be used as refractory? Alumina has a melting point of more than 2000 degrees and a boiling point of more than 2900 degrees. It is a high-quality refractory raw material.
Alumina can usually be used as high-temperature refractory materials. Generally speaking, fireproof materials are required to have flame retardancy and flame retardancy in addition to being non combustible. Therefore, aluminum oxide is usually included in the general sense of fireproof materials.
What is alumina?
Aluminum oxide, chemical formula Al2O3. It is a kind of high hardness compound, with a melting point of 2054 ℃ and a boiling point of 2980 ℃. It is an ionic crystal that can be ionized at high temperatures and is commonly used to make refractories.
Aluminum oxide is a stable oxide of aluminum, with the chemical formula of Al2O3. It is also called bauxite in mining, ceramics and material science.
Industrial alumina is prepared from bauxite (Al2O3 · 3H2O) and diaspore. Al2O3 with high purity requirements is generally prepared by chemical methods. Al2O3 has many homogeneous and heterogeneous crystals. There are more than 10 known types, mainly including 3 crystal forms, namely α- Al2O3、 β- Al2O3、 γ- Al2O3。 Among them, different structures and properties are also different, and almost completely convert to α- Al2O3。
At present, the main raw material for the production of special alumina products is industrial alumina, which is the intermediate product of aluminum smelting industry. Its true density is 3.60g · cm-3, and the mineral composition is γ– Al2O3。 Industrial alumina is white powder.
When manufacturing special pure products, raw materials with Al2O3 content greater than 99.8% or raw materials made from aluminum sulfate and ammonia sulfate shall be used.
It is difficult to sinter industrial alumina. In order to improve the sintering temperature, it is necessary to finely grind and pre burn the raw materials, and add additives to promote sintering.
Industrial alumina should be pre fired at 1350~1600 ℃ before use to accelerate γ- Alumina orientation α- 3% boric acid is added to accelerate the transformation of alumina into α- Al2O3 can also reduce the pre sintering temperature, shorten the holding time and improve the purity of raw materials (Na2O and H3BO3 in raw materials generate volatile compound sodium borate, which is removed together). The disadvantage is that the material becomes hard after burning and is not easy to be finely ground.
Grinding fineness plays an important role in the sintering and recrystallization of green bodies.
Calcined alumina is a kind of refractory material with excellent performance obtained by calcining pure alumina at high temperature. It can be made into coarse particle material, fine particle material, fine powder and micro powder, and can be used to make pure corundum fired products. For example, corundum brick, light corundum brick. It can also be used with other raw materials, such as carbon materials, to make various unburned products. For example, aluminum carbon, aluminum zirconium carbon materials. As for making amorphous refractory, there are more kinds. It can be made of corundum, chrome corundum and corundum spinel, and it can also be added to other materials to improve various specific properties. It is not limited to high alumina castables, but can be castables, ramming materials, plastic materials, gunning materials and refractory mud.
Alumina is one of the most mature high melting point oxides. Its raw materials are abundant, cheap, and have many excellent properties. Therefore, alumina is a widely used oxide refractory in refractory plants. The Mohs hardness of alumina is 9, which is lower than that of diamond and some refractory compounds. Alumina refractories have very high mechanical strength. The flexural strength at room temperature is 250MPa, and it still has 150MPa at 1000 ℃. The compressive strength at room temperature can be more than 2000MPa. The compressive strength of some products with microcrystalline structure can even reach 5000MPa.
The refractoriness of alumina refractories is greater than 1900 ℃, and the starting point of 0.2MPa load softening is about 1850 ℃. Its limiting service temperature is 1950 ℃, and the commonly used temperature is 1800 ℃. The average linear expansion coefficient of alumina at 20-1000 ℃ is 8.6 × 10-6/℃。 The thermal conductivity of aluminum oxide at room temperature is half that of aluminum metal, and the thermal conductivity decreases with the increase of temperature.
The thermal shock resistance of alumina refractory depends on its microstructure and the shape and size of the product. Generally speaking, its thermal shock resistance is medium. In a word, aluminum oxide has high temperature resistance, high strength, high hardness, oxidation resistance, electrical insulation, corrosion resistance, good air tightness and other properties. Therefore, it is widely used as a special refractory. The typical use is to use its high temperature resistance, corrosion resistance, high strength and other properties as sliding nozzle, immersion nozzle, crucible for metallurgical high-purity metal or single crystal growth in steel production, as well as various high-temperature furnace structures (furnace wall, furnace tube), heat resistance and oxidation resistance coating, etc.
Can alumina be used as a refractory material?
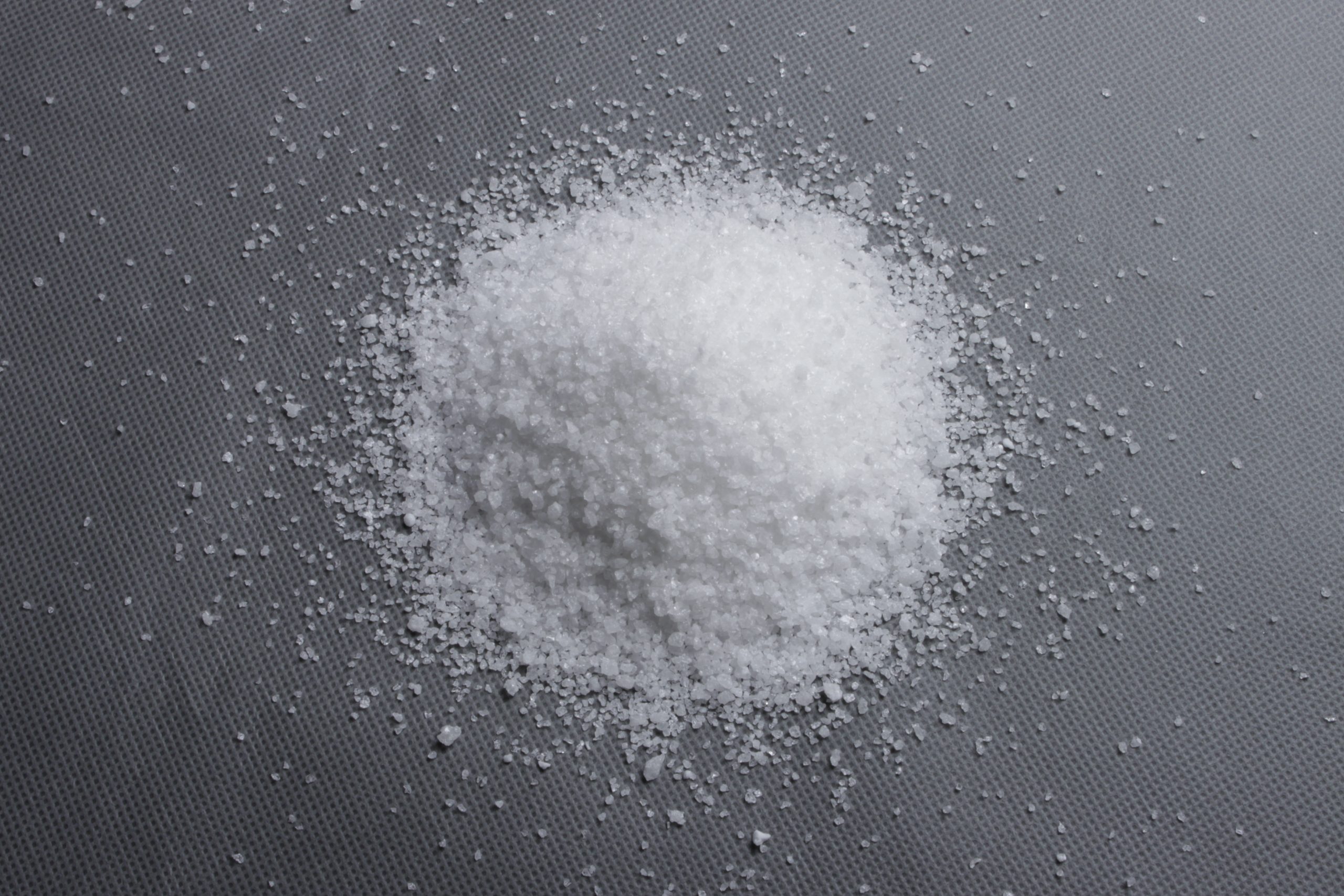