What is ramming material?
Compared with the amorphous refractories of other similar materials, the ramming materials are dry or semi dry, and most materials are not bonded before forming, so the dense structure can be obtained only through strong tamping. Most ramming materials have low strength at room temperature before sintering, and some have low strength at medium temperature. Only after sintering or coking of the carbonaceous compounds in the binder during heating can strong bonding be obtained.
The fire resistance and corrosion resistance of ramming materials can be obtained by selecting high-quality refractory materials and adopting correct proportion and strong tamping. Compared with castables and plastics, it has higher stability and corrosion resistance at high temperatures. However, its service life depends to a large extent on the pre sintering before use or the sintering amount at the first use. If the heating surface is sintered as a whole without cracking and separation from the bottom layer, the service life can be improved.
In addition to construction at room temperature, when thermoplastic organic materials that can form carbon are used as adhesives, the method of hot mixing is usually used. The construction shall be carried out immediately after the mixing is even.
After forming, different heating methods are used to promote the hardening or sintering of the mixture according to its strengthening characteristics. For those who contain inorganic chemical adhesives, the mold can be removed for baking after the hardening reaches a certain strength; For people with thermoplastic carbon adhesive, demoulding is carried out after the cooling strength is quite high. After demoulding, it shall be heated quickly to make it coking before use; For those who do not contain hardened adhesives at room temperature, they are often sintered with moulds after tamping. For example, just add 1% silicone? When 2% boric acid is used to manufacture inductive furnace lining, the mixture shall be filled into the iron core mold, tamped, and then electrically heated for sintering. The sintering of tamping furnace lining can be carried out in advance before use, and appropriate heat treatment can be adopted for the first use.
Ramming materials are mainly used as lining materials for various smelting furnaces in direct contact with molten materials. In addition to forming the whole furnace lining, it can also be used to manufacture large products.
Corundum ramming material
Corundum ramming material is a fire-resistant ramming material, which is classified according to the aggregate variety. That is, aggregate and powder are composed of fused corundum or sintered corundum. Suitable for water glass, cement, phosphate, phosphate, aluminum sulfate, clay and other adhesives. As corundum is an advanced refractory, phosphate, phosphate and pure aluminate cement are usually used as adhesives, and appropriate additives are added. The particle composition and adhesive type of the raw material are almost the same as those of the corundum castable, but compared with the castable, the water consumption or the amount of chemical adhesive is reduced by 1/3~1/2. If phosphoric acid and magnesium chromate are combined with corundum mud, the mud moisture is less than 10%; During wet tamping, the moisture content of mud is 3%, and that of castable is 5%~7%. The properties of the castable are better than those of corundum castable due to its low water content and tight knot.
According to the operating conditions of the carbon black reactor, our research institute has studied the use of corundum as the main raw material, with active micro powder, additives and adhesives, in the carbon black plant reactor. The service life is more than twice that of the original low purity jade brick.
With the continuous development of metallurgy and petrochemical industry, corundum ramming material will become a new product with considerable development prospects. However, the construction speed of ramming materials is slow, the labor intensity is high, and the labor efficiency is low. Therefore, the development of ramming materials is slow in recent years, and there is a tendency to be replaced by corundum dry vibrating materials and high-quality corundum casting materials. Corundum ramming material has been used in ladle lining, blast furnace taphole, top of electric steelmaking furnace, power frequency induction furnace, external refining device and other thermal equipment, and has achieved certain results. At present, castables and prefabricated blocks are widely used in ladle lining. The iron trench of large blast furnaces such as Baosteel has been replaced by castables of the same material. However, some blast furnaces, especially small and medium-sized ones, are still very common.
How to construct corundum ramming material?
1、 Site construction
The on-site construction of corundum ramming material can be carried out according to the following steps: first, correctly position the breathable brick. During the construction of bottom package materials, 60 pieces of mm~80 shall be reserved between the air brick base brick and the bottom package brick
Mm gap is used as the joint filling area. After the construction of packaging materials is completed, pour the mixing materials into the mixer, add clean tap water and start mixing. In the process of mixing, add water without forming a spherical block, and hold the ball with your hand instead of dispersing it.
After min, determine whether the ramming material is mixed evenly, and then lift it into the ladle to start construction.
First, clear the sundries in the reserved joint filling area, add about 1/3 of the height of corundum ramming material, and tamp it evenly with an air pick, then add the ramming material to 1/2 of the height, and continue to tamp. At the same time, the process of tamping and feeding shall be carried out. Repeated addition shall be carried out. More than 4 layers of rotary tamping shall be carried out, and the surface shall be tamped firmly. When each layer of material is tamped, the surface of the lower layer of material shall be 3 wide
Mm, 10mm~20mm deep, four scratches on each side to ensure that each layer of ramming material is closely combined. The tamping process must be carried out continuously, and each tamping time shall be controlled within 10m
in。 After tamping, tamp the joint surface between the base brick and the bottom brick into a slope. After the construction is completed, the ladle can be baked online according to the normal process.
2、 Field application
This kind of corundum ramming material is used for field application in t steel packaging of the steelmaking plant of Benxi Iron and Steel Co. In the test, 10 steel ladles were selected, mainly recording the blowing rate and service life of the porous brick after the corundum ramming, and the use of the porous brick without the corundum ramming and caulking under the same conditions. The test results are shown in Table 1. The data in the table are the average of the statistical data.
After tamping and caulking with corundum, the blowing rate and service life of the ladle vent brick have been greatly improved. The permeability brick rate is 84.0%, which is increased to 99. The service life of the permeability brick is increased by 16%. 8%. The use of corundum ramming material can greatly improve the performance of the porous brick.
It can be considered that the corundum ramming material has played an effective role in protecting the porous brick during use, and has eliminated the influence of thermal expansion of the bottom covering brick on the shear stress of the porous brick. Specifically, due to the difference in performance between the breathable brick and the bottom covering brick, their use performance is quite different. In order to ensure the stability of argon flow, the thermal expansion coefficient of porous brick under high temperature is very low, generally not more than 0.05%. The thermal expansion coefficient of the brick at the bottom of the bag is generally 1%~2% [2], which requires a certain expansion during use to improve the integrity of the bottom of the bag, so as to improve the overall service life of the bottom of the bag. At high temperature, due to the expansion of the bottom cladding brick, the air permeable brick is squeezed greatly, resulting in considerable transverse shear stress. In severe cases, it will lead to the fracture of the air permeable brick seat brick, which is easy to peel off during use, leading to the fracture of the air permeable brick core, resulting in air leakage and backflow, affecting the use of the air permeable brick. This problem can be alleviated and solved by using corundum ramming material to fill the joints, adding a buffer layer between the breathable brick and the bottom brick to avoid direct contact, and eliminating the shear stress between the breathable brick and the bottom brick.
In addition, after using corundum ramming material, when replacing the air permeable bricks in the ladle, it is only necessary to remove the ramming material to take out the remaining air permeable bricks without damaging the overall structure of the bottom of the ladle, thus reducing the construction difficulty and improving the construction efficiency.
Refractory castable manufacturer: performance and construction of corundum ramming material
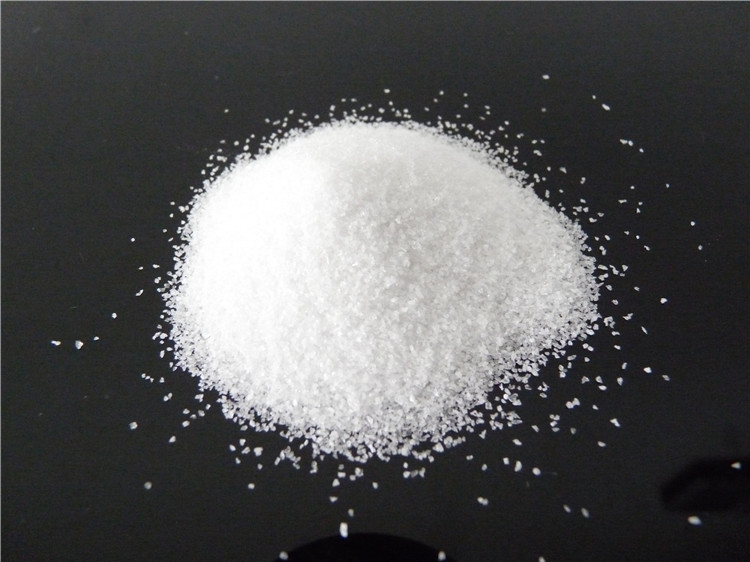