Refractory concrete is an amorphous refractory material that is prepared by adding water or other liquids to refractory aggregates, powders and cements and directly used without calcination. It is also called refractory castable, and is usually constructed by pouring.
Causes of cracks in refractory concrete
Cracks in refractory concrete are caused by the following reasons:
(1) The water cement ratio is too large, resulting in pores and cracks on the surface;
(2) Excessive cement consumption, shrinkage cracks;
(3) Poor or untimely maintenance, surface dehydration, drying shrinkage cracks;
(4) The slump is too large, the pouring is too high and too thick, and the floating surface of plain mortar is cracked;
(5) The formwork is removed too early, and the concrete is pried off with improper force;
(6) The concrete surface is not compacted;
(7) The protective layer of reinforcement is too thin and cracks along the reinforcement;
(8) Lack of stirrups and temperature bars makes the concrete crack;
(9) There is no measure to reduce the internal and external temperature difference for mass concrete;
(10) There is no reinforcement at the corner of the opening where the application is concentrated.
(11) The causes and characteristics of concrete cracks.
1. Classification of refractory concrete:
① Ordinary refractory concrete. The aggregates used include high alumina, clayey, siliceous, alkaline materials (magnesia, chromite, dolomite, etc.) or special materials (carbon, silicon carbide, zircon, etc.), and several combinations of refractory aggregates can also be used.
② Insulated refractory concrete. It is mainly prepared with fire-resistant light aggregate. The light aggregates used include expanded perlite, vermiculite, ceramsite, porous clay clinker, hollow alumina ball, etc. They can also be combined with several refractory light aggregates or with refractory aggregates.
Cements used for refractory concrete include high alumina cement, phosphate cement, water glass cement, clay, etc.
Advantages of refractory concrete: refractory concrete is a non fired product, with simple production process and energy saving. It can be poured into any shape according to the construction position. Its integrity is better than that of refractory brick lining. It is suitable for mechanized construction. Regular inspection and maintenance can prolong the life of furnace lining. Refractory concrete is mainly used in metallurgical, petroleum, chemical, building materials, machinery and other industrial kilns. The general operating temperature is 1300~1600 ℃. The refractory concrete with the temperature lower than 900 ℃ is called heat-resistant concrete, which is mainly used in the foundation, chimney, flue and other structures of thermal equipment.
2. Advantages of refractory concrete:
The refractory concrete is a unburned product with simple production process and energy saving. It can be poured into any shape according to the construction position. Its integrity is better than that of the refractory brick lining. It is suitable for mechanized construction. Regular inspection and maintenance can prolong the life of the furnace lining. Refractory concrete is mainly used in metallurgical, petroleum, chemical, building materials, machinery and other industrial kilns. The general operating temperature is 1300~1600 ℃. The refractory concrete with the temperature lower than 900 ℃ is called heat-resistant concrete, which is mainly used in the foundation, chimney, flue and other structures of thermal equipment.
3. The advantages and characteristics of refractory concrete compared with refractory bricks are as follows:
(1) The refractoriness is similar to that of refractory bricks of the same material. However, since the refractory concrete (castable) has not been sintered and shrinks greatly during initial heating, the load softening point is slightly lower than that of refractory bricks.
(2) The compressive strength of refractory concrete at room temperature is high due to the role of low-temperature cementitious materials. At the same time, because of the good integrity of the masonry, the furnace has good air tightness and is not easy to deform, and the furnace has better mechanical vibration and impact resistance than the brick masonry. For example, the upper part of the side wall used for soaking pit is subject to severe mechanical wear and collision, and its service life is several times longer than that of the brick.
(3) The thermal stability is good. The main materials (refractory aggregate and powder) used are all clinker calcined at high temperature. The expansion and shrinkage of the cement counteract each other. Therefore, the thermal expansion of the masonry is relatively smaller than that of the refractory brick, and the temperature stress is also small. In addition, there are various reticulated, needle shaped and chain shaped crystalline phases in the structure. Strong resistance to low temperature stress. For example, it is used to cast the mouth and cover of soaking pit, and the service life is extended to one and a half years.
(4) The production process is simple, and the complicated brick making process is canceled. After formwork erection, casting, molding, curing and baking, it can be put into production and used. It can be made into various prefabricated blocks and can be mechanically constructed, greatly speeding up the furnace building speed and more than ten times higher than the brick laying efficiency.
The difference between high temperature coating material and refractory coating material
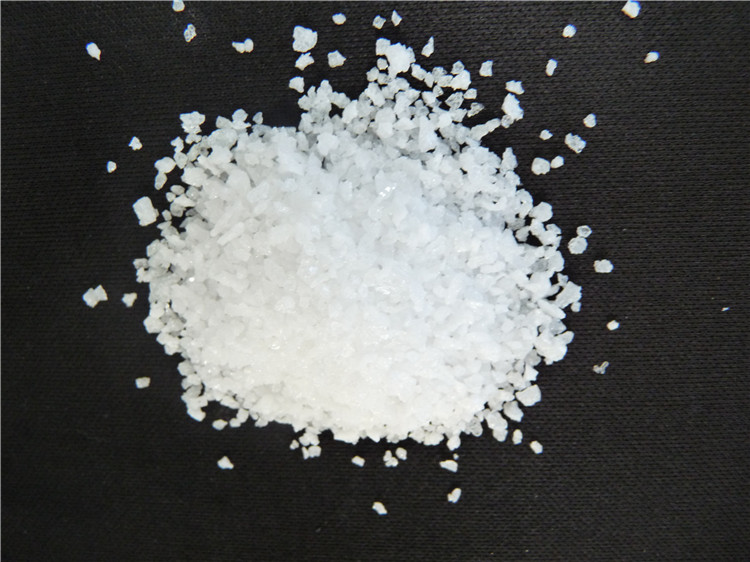